Motor Control Panel
Each MCC shall consist of vertical sections made of the welded side-frame assembly formed from a minimum of 12 gauge steel. Internal reinforcement structural parts shall be of 12 and 14 gauge steel to provide a strong and rigid construction
MCC FINISH
All steel parts shall be provided with acrylic/alkyd baked enamel paint finish or Powder Coat, except plated parts used for ground connections. All painted parts shall undergo a multi-stage treatment process, followed by the finishing paint coat.
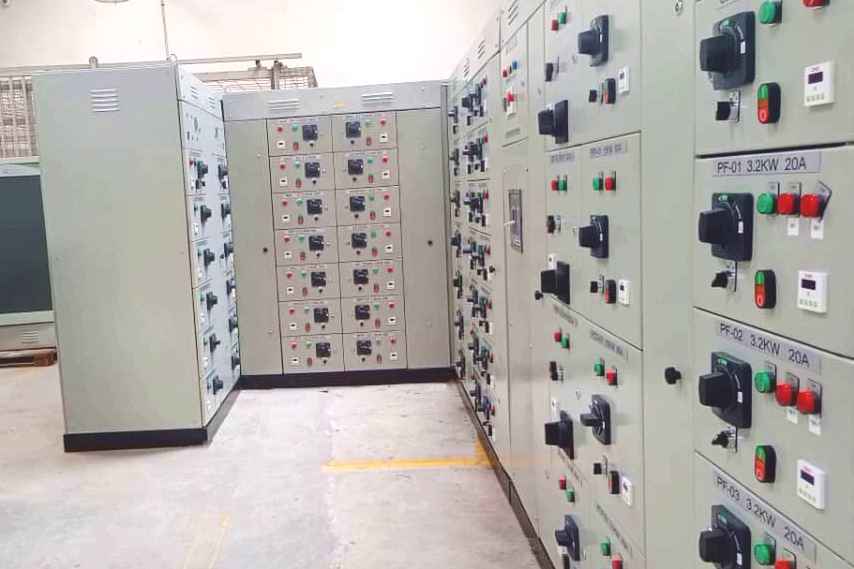
Pre-treatment shall include:
- Hot alkaline cleaner to remove grease and oil.
- Iron phosphate treatment to improve adhesion and corrosion resistance.
- The paint shall be applied using an electro-deposition process to ensure a uniform paint coat with high adhesion.
- The paint color shall be epoxy medium light gray. Unit interior saddles shall be painted orange.
TYPICAL UNIT CONSTRUCTION
All conducting parts on the line side of the unit disconnect shall be shrouded by a suitable insulating material to prevent accidental contact with those parts.
A lever handle operator must be provided on each disconnect. With the unit stabs engaged onto the vertical phase bus and the unit door closed, the handle mechanism shall allow complete ON/OFF control of the unit. All circuit breaker operators shall include a separate TRIPPED position to clearly indicate a circuit breaker trip condition. It shall be possible to reset a tripped circuit breaker without opening the control unit door. A clear indication of disconnect status shall be provided, by adhering to the following operator handle positions:
- Handle “On” position must be up or to the left and within 45 degrees of being parallel to the face of the equipment.
- Handle “Off” position must be down or to the right and within 45 degrees of being parallel to the face of the equipment.
- The minimum separation between the “On” and “Off” positions shall be 90 degrees.
- On Circuit Breaker disconnects, the handle “Tripped” position must be perpendicular to the face of the equipment +/- 30 degrees. The minimum separation between “On” and “Tripped” shall be 30 degrees. The minimum separation between “Tripped” and “Off” shall be 45 degrees.
A mechanical interlock shall prevent the operator from opening the unit door when the disconnect is in the ON position. It shall be possible for authorized personnel to defeat these interlocks.
COMPONENTS FOR TYPICAL UNITS
a. Combination Starters
- All combination starters shall use NEMA/EEMAC rated contactors. Starters shall be provided with a three-pole, external manual reset, overload relay with thermal overload units.
- When provided, control circuit transformers if utilized shall include two primary protection fuses and one secondary fuse (in the non-ground secondary conductor). The transformer shall be sized to accommodate the contractor(s) and all connected control circuit loads. The transformer rating shall be fully visible from the front when the unit door is opened.
- When a unit control circuit transformer is not provided, the disconnect shall include an electrical interlock for the disconnection of externally powered control circuits.
- Auxiliary control circuit interlocks shall be provided where indicated. Auxiliary interlocks shall be field convertible to normally open or normally closed operation.
b. Terminal Blocks
- When Type B wiring is specified, all starter units shall be provided with unit control terminal blocks.
- Terminal blocks shall be the pull-apart type with a minimum rating of 250 volt and 10 amps. All current-carrying parts shall be tin-plated. Terminals shall be accessible from inside the unit when the unit door is opened. Terminal blocks shall be DIN rail mounted with the stationary portion of the block secured to the unit bottom plate. The stationary portion shall be used for factory connections and shall remain attached to the unit when removed. The terminals used for field connections shall face forward so they can be wired without removing the unit or any of its components.
c. Nameplates
- Shall be engraved phenolic nameplates for each MCC and unit compartment. Shall be gray background with white letters, measuring a minimum of 1.5 in (38 mm) H x 6.25 in (159 mm) W total outside dimensions.
d. Pilot Device Panel
- Each starter unit shall be proved with a hinged/removable control station plate, which can accommodate up to five 22 mm pilot devices or three 30 mm pilot devices
ADJUSTABLE FREQUENCY AC DRIVE UNIT CONSTRUCTION
All AC drive controller units shall be provided with unit control terminal blocks for use in terminating field wiring.
The AC drive controller unit shall incorporate a self-contained, air-based cooling system where required. Any air exhaust vents shall be louvered to help direct airflow away from personnel operating the AC drive controller unit. Any fans, ductwork, or filters shall be easily accessible for maintenance.
Cooling
- The AC drive controller unit cooling system shall be sized to cool the drive regardless of mounting location within the MCC. The AC drive controller unit shall not be restricted to a specific location in the MCC.
- An internal over-temperature trip shall be provided to detect cooling system failure or blockage. Upon the occurrence of an over-temperature trip, the cooling system fans shall continue running to provide a rapid cool down.
- Power for the cooling system shall be provided internal to the AC drive controller unit by use of a control power transformer that includes two primary fuses and one secondary fuse (in the non-ground secondary conductor).
Protection
- The AC drive controller unit shall be protected against fault currents
- The AC drive controller unit shall be protected against short circuits between output phases, between output phases and ground, on the internal power supplies.
- Upon loss of the analog process follower reference signal, the AC drive shall be programmable to a fault and freewheel stop, ramp stop, fast stop, stop without the trip, automatically restart, run at last speed, or maintain a user-defined low-speed setting.
- The AC drive shall include an adjustable thermal alarm which can be assigned to a relay or logic output to indicate the drive temperature has reached the thermal alarm setting.
Graphic Display Terminal Interface
- The AC drive model number, torque type, software revision number, horsepower, output current, motor frequency, and motor voltage shall all be listed on the drive identification display as viewed on the graphic display terminal.
CONTROL & COMMUNICATION
- Pilot devices shall be industrial-rated [22mm] [30mm] type control operators and used independently of the keypad display. Software assignments for control inputs and outputs to operate factory-supplied controls shall be pre-configured from the factory. The following basic controls shall be provided:
- [HAND-OFF-AUTO selector switch – The HAND mode shall allow manual operation of start, stop, and speed control.
- The AC drive shall start when the control operation is in HAND mode.
- A door-mounted, manual-speed potentiometer shall be used to control speed in the HAND mode.
- The AC drive shall run at the low-speed setting or higher as required by the position of the manual-speed potentiometer. This mode shall function as 2-wire control and automatically restart after a power outage or auto restart after a fault. The OFF position of the control operation shall stop the AC drive and prevent it from restarting.
- The AUTO (automatic) mode shall receive an [auto start contact] [serial link command] to control starting and stopping of the AC drive. This contact shall also start and stop bypass (if used) when both the automatic and bypass modes of operation are selected.
- Speed control shall be from a customer supplied [4–20 mAdc] [serial link communication] signal.]
- [START-STOP pushbuttons—START/STOP pushbuttons shall provide 3-wire start/stop control.]
- [POWER On pilot light, red]
- [FAULT pilot light, yellow, push-to-test]
- [RUN pilot light, green, push-to-test]
- [STOPPED pilot light, red, push-to-test]
- [HAND/AUTO pilot lights, yellow, push-to-test]
- NOTE: Additional controls can be found on the equipment electrical diagrams.
- Drives shall include a network communication interface for data acquisition only over [Modbus] [Modbus Plus] [Ethernet (Modbus TCP)] [DeviceNet] [PROFIBUS DP]. Drive control and speed control via PLC hardwired I/O shall include:]
- [PLC Analog output (4–20 mA) speed reference signal]
- [PLC Analog input (4–20 mA) speed feedback signal]
- [PLC digital output drive start control] [PLC digital outputs for drive preset speed control]
- [PLC digital input drive run (Run =1)]
- [PLC digital input drive fault (Fault = 1)]
- Drives shall include a network communication interface for control and data acquisition over [Modbus] [Modbus Plus] [Ethernet (Modbus TCP)] [DeviceNet] [PROFIBUS DP] [Ethernet IP].
[At a minimum, drive units shall allow configuration of these parameters:]
- [Motor Frequency]
- [Motor Voltage]
- [Ramp Profiles]
- [I/O Assignments]
- [Current Limitation]]
Drive units shall be capable of making these adjustments:]
- [Speed Range]
- [Ramp Time]
- [Thermal Protection]
Drive units shall allow control of these parameters:]
- [Start/Stop]
- [Braking]
- [Frequency Reference]
- [Fault Resets]
Optional Harmonic Provisions
- A harmonic distortion analysis shall be performed and priced as a separate line item by the AC drive manufacturer based upon system documentation supplied by the contractor. The documentation shall consist of one-line diagrams, distribution transformer information (kVA, %Z, and X/R ratio), and emergency standby generator performance specifications. The harmonic distortion analysis report shall be part of the approval drawing process, submitted to the engineer for approval. If the calculations determine that harmonic distortion values are higher than the voltage and current values specified in IEEE 519-1992, the drive manufacturer shall provide line reactors of sufficient percent impedance to meet the IEEE specified values. The line reactor shall be ventilated in the MCC and shall be completely factory wired and tested with the AC drive controller unit.
- 2. A 3-5% impedance line reactor shall be provided that is completely factory wired and tested with the AC drive controller unit.
- 3. An active harmonic filter shall be provided to perform electronic cancellation of load-produced harmonic currents such that the upstream power harmonic current and voltage are reduced below the IEEE 519-1992 guidelines for load demand and voltage distortion limits. Filter shall be Square D® brand Accusine or equivalent. Performance of the filter shall be independent of the impedance of the power source: AC lines or backup generator. All necessary current transducers, reactors, and operator interfaces shall be supplied with the MCC. A factory-certified start-up technician shall be used to start up each harmonic filter to achieve optimum system performance.
General Communication Cabling
- The MCC shall employ a pre-engineered communication cabling system to interconnect units within the MCC.
- Network cabling shall be routed through the lower horizontal wireway to isolate the network from the horizontal bussing routed through the top.
- The full-depth vertical wireway serves to separate communications from power cabling to prevent noise interference on the network cable.
- The communication cabling installation shall meet Class 2 wiring practices under the provisions of NEC articles 725 and 800.
- Provisions for appropriate terminators and grounding shall be provided.
- Addition, removal, or rearrangement of units shall not interrupt the trunk line and shall not affect the cabling of other units attached to the trunk line.
- Cable assemblies will use 5-pole Micro-style connectors with a single keyway and will comply with SAE-H1738-2 specifications.
- Connectors are to be epoxy-coated for a 500-hour salt-spray test per Mil-Std 202F.
- The cable coupler design shall include a vibration-resistant ratchet to prevent loosening.
- The system will be constructed of molded PVC material.
Modbus® Communication Cabling
- The Modbus cabling system will be UL 498 Listed.
- An extended ground pin shall ensure first make/last break ground connections.
- The cabling system shall consist of individual trunk line segments in each MCC section. A trunk/drop topology will be used. Trunkline segments will be routed from the lower wireway into each vertical section. The trunkline for sections containing plug-on vertical bus shall have six taps spaced 12 in. apart. Unused tee connectors will be capped at the factory.
- A 36-in. (915 mm) “pigtail” cable shall connect the communication device in each MCC unit to the trunk cable via a pre-engineered tap. One end of the pigtail cable will terminate in a Micro-style connector and will be attached to the trunk. The other end will terminate at the communication device in the MCC unit.
Ethernet (Modbus TCP) Communication Cabling
- The Ethernet (Modbus TCP) communications network shall be configured in a star topology.
- The cabling system shall consist of multiple, custom-length Ethernet patch cables that each connect a single network device to a central Ethernet switch unit located in the MCC.
- Ethernet switches located in the MCC shall be Connexium, Hirschmann, or approved equal.
PROFIBUS DP Communication Cabling
- The PROFIBUS DP cabling system shall consist of individual trunk line segments in each MCC section. A trunkline-dropline topology will be used. Trunkline segments will be routed from the lower wireway into each vertical section. The trunkline for sections containing plug-on vertical bus shall have six taps spaced 12 in. apart. Unused tee connectors will be capped at the factory.
- Sectioned cabinets shall have six pre-molded trunklines with tees. Full-length cabinets shall have one trunkline with a tee. A tee at the bottom of each section shall provide the means of connection to the next section with a pre-molded section of cable.
- A 36-in. (915 mm) “pigtail” cable shall connect the tee in the dropline to the PROFIBUS DP device located in the MCC unit.
- Each device shall be configured and addressed to correspond with software settings.
QUALITY CONTROL
The entire MCC shall go through a quality inspection before shipment. This inspection will include:
1. Physical Inspection of:
a. Structure.
b. Electrical conductors, including:
- bussing.
- general wiring.
- units.
2. Electrical Tests
a. General electrical tests include:
- power circuit phasing.
- control circuit wiring.
- instrument transformers.
- meters.
- ground fault system.
- device electrical operation.
b. AC dielectric tests shall be performed on the power circuit.
3. Markings/Labels, include:
- instructional type.
- Underwriters Laboratory (UL)/Canadian Standards Association (CSA).
- inspector’s stamps.
4. Each device shall be configured and addressed to correspond with software settings.
5. A Read/Write test shall be performed prior to shipment on all network devices including, but not limited to, Overloads, Drives, and Soft Starters.
6. Testing shall be designed to verify system operation and shall include these verifications as a minimum:
- Drawings and Bill of Materials
- I/O addressing
- Correct device operation by I/O address
- Host Communications
- Control Network Interface
7. The manufacturer shall use integral quality control checks throughout the manufacturing process to ensure that the MCC meets operating specifications.